Improving the Observation and Evaluation of Tablets and Tableting Machines
Tablets are widely used because they hold the active ingredient in a pharmaceutically produced, solid, and fixed shape. They are also portable, can be stored for a long time, and make it easy to recognise the dosage.
This section explains the process to produce tablets, common defects in tablet products, and the countermeasures to these issues.
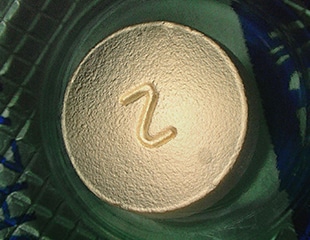
- Tablet Moulding (Tableting) Process with a Tableting Machine
- Tablet Defects (Tableting Malfunctions and Quality-characteristic Errors)
- Observation and Measurement Examples of Effectively Inspecting the Quality of Tablets
- A Digital Microscope That Improves the Quality Assurance of Tablets
Tablet Moulding (Tableting) Process with a Tableting Machine
Tablets are produced by subjecting ingredients in powder form to compression moulding. They are widely used in medical products designed to be taken internally. If there are no problems with the quality of a tablet, it is just as effective when the medicine is taken in its original granular form. The main factor that affects the quality of a tablet during its production is its moulding (tableting) process.
Tableting machines are the devices used in the tableting process. Equipped with moulds, they are a type of press and are also called rotary moulding machines. The added powder ingredient is automatically weighed and inserted into the hole in the die, the fixed mould. Then, the mould known as the punch applies pressure to the powder from above and below, moulding it into a tablet. In mass production of tablets, the filling with powder material, compression with the mould, and discharging of the tablet are performed continuously.
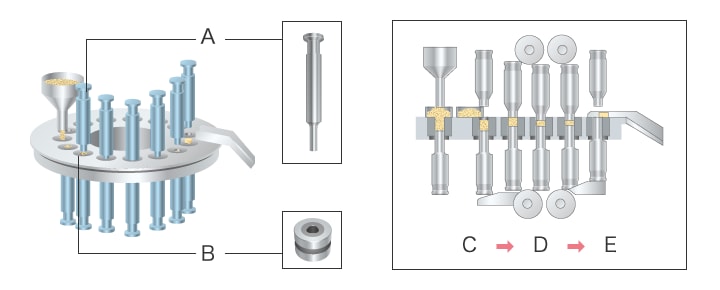
- A
- Punch
- B
- Die
- C
- Filling
- D
- Compression
- E
- Discharging
Tablet Defects (Tableting Malfunctions and Quality-characteristic Errors)
Defects on the outside or inside of a tablet change its storage status which impairs the quality of the product, decreases its reliability and safety, and leads to complaints from customers.
When using a tableting machine, the internal structure may not be uniform due to varying internal density caused by mechanical stress and there may be scratches, chips, and other defects on the outside of the tablets due to low external density or mould wear. These issues may lead to quality deterioration and the intended results won't be obtained due to changes in characteristics.
Causes and types of tableting malfunctions
Malfunctions in the tableting process can cause defects in tablets, most often due to the properties of the principal agent. The cause is most often the properties of the principal agent in the medicine. For example, if distributed on the surface of the tablet, this agent will come into direct contact with the metal surfaces of the tableting machine’s punch and die, possibly changing the characteristics of this agent. This is a typical tableting malfunction caused by the inclusion of an inappropriate amount of binding agent.
This defect can be classified according to the amount of binding agent as follows.
Insufficient binding agent
This can cause capping (in which the top or bottom surface of the tablet comes off) and lamination (in which the main body of the tablet comes off).
Excessive binding agent
This can cause defects such as sticking (in which a part of the material affixes to the contact surface of the punch and comes off), picking (in which a small amount of material affixes to the contact surface of the punch, causing patchy strips in tablets), and binding (in which vertical scratches occur on the sides of tablets).
Quality-characteristic errors
This is another typical problem in tableting and includes decreased hardness (in which tablets are softer than intended due to uneven distribution) and delayed dissolution (in which the dissolution property decreases, which is the opposite problem of decreased hardness). These quality-characteristic errors cause tablets to dissolve with unintended timing in the gastrointestinal tract after the patient takes the medicine, causing it to be absorbed by this tract too early or too late. Hence, the internal medicine does not have its intended effect.
Importance of tablet defect countermeasures
The first countermeasure against these tableting defects and problems when taking medicine is to ensure the hole in the die is filled with the appropriate amount of material. Changes to the characteristics can also be avoided by distributing the binding agent on the surface of the tablet (the die side), preventing the principal agent in the medicine from coming into contact with the die. Sufficient consideration must also be given to the response to water during tablet storage and when taking the medicine.
As such, tablet quality assurance requires that the causes and problems of tablet defects be investigated and eliminated through observation of the outer appearance of tablets. Therefore, clear magnified observation and evaluation through quantitative measurement of the outer appearance and cross sections of tablets are very important.
Observation and Measurement Examples of Effectively Inspecting the Quality of Tablets
Tablets are small and three dimensional, which makes it difficult to bring them entirely into focus during magnified observation. Also, determining the appropriate lighting conditions for observation of microscopic surface conditions is very difficult and takes a lot of time and effort. Furthermore, tablets formed from powder by compression moulding are delicate, so it is not realistic to expect contact measuring instruments to be able to measure tablets in 3D.
KEYENCE’s VHX Series digital microscope eliminates conventional problems by allowing operators to automatically adjust focus and lighting conditions to capture fully-focused, high-resolution images. The system also ensures that accurate measurements can be quickly captured for analysis, improving the efficiency in quality control and assurance.
Read on for the latest observation and measurement examples of tablets using the VHX Series.
Observation of a tablet through a PTP
The VHX Series 4K digital microscope provides a depth of field that is at least 20 times larger than optical microscopes, capturing fully focused images of the entire tablet, even if it is contained in a PTP (press through package).
Imaging tablets through PTP can be difficult due to the light reflections; but by using the ring-reflection removal function, users can clearly observe the surface irregularities on tablets.
This tool is useful for capturing defects and identifying the process in which the tablets were scratched or chipped.
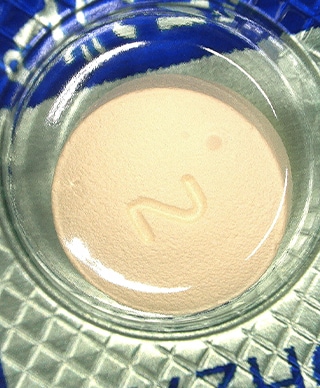
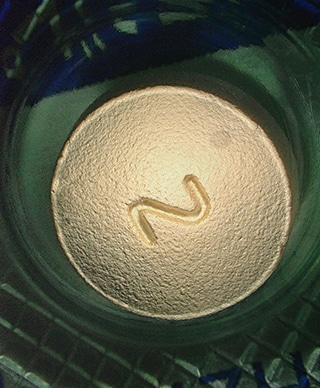
Observation of microscopic surface roughness on the cross section of a tablet
Observation of tablet cross sections is vital in investigating the density of tablets and the distribution of ingredients during tableting. However, most tablets consist of a single light colour, which makes it easy for glare to occur. Therefore, using conventional microscopes was time-intensive and difficult to determine the optimal lighting conditions.
The VHX Series 4K digital microscope is equipped with a Multi-lighting function that automatically acquires data captured with omnidirectional lighting at the press of a button. The operator just has to select the optimal image from all those that have been acquired, eliminating the time and effort that were conventionally wasted on repeated lighting condition determination. The optimal images for observation of microscopic surface irregularities can now be easily obtained even when observing low-contrast tablet cross sections.
Furthermore, lighting data is saved even after images are recorded, so observation under the same lighting conditions can be performed immediately with no need to determine its conditions again. This allows operators to view samples under the same lighting conditions while minimising the risk for error.
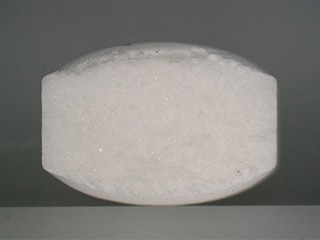
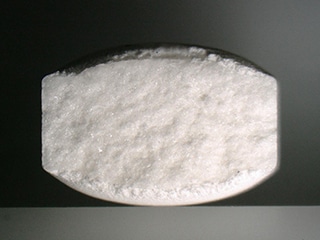
3D observation of the wear status of a tableting machine’s punch tip
To reduce the occurrences of defective products in the mass production of tablets, it is important to understand the status of tableting machines. Wear on the surface of the punch tip—which acts as a mould and continually contacts the materials, compressing them inside the die—may lead to poor stamping of text information such as the medicine name and dosage, so it is necessary to check the status of punch tips through periodic observation. However, the surfaces of these tips are small, and the surface irregularities used to stamp text have microscopic shapes, so it was difficult to observe these shapes in three dimensions.
The VHX Series digital microscope can capture microscopic shapes and surface conditions while changing the focus position, allowing for observation with 3D images and accurate measurements.
The 3D-displayed stamping surface of the punch tip can be rotated in any direction for efficient observation of microscopic shape changes and surface conditions. Accurate 2D/3D measurements can be easily captured and recorded, making it possible to find trends in wear.
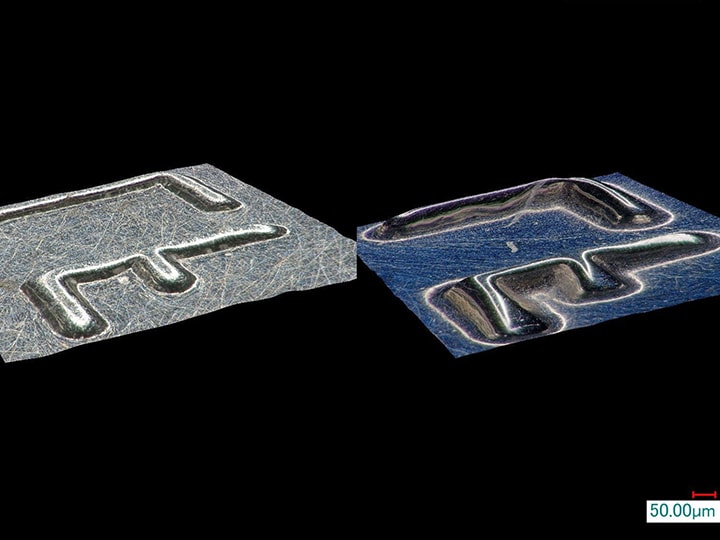
Observation and measurement of the inner surface of a tableting machine’s die
During tableting, the tableting machine’s die moulds the sides of the tablet. Scratches on the die are projected onto the sides of the tablet, so checking the internal surfaces of the die is vital to maintaining quality. However, it is very difficult to observe the surface conditions of deep parts at high magnifications and in a non-destructive manner.
The VHX Series 4K digital microscope is equipped with a Multi-lighting function that automatically acquires image capturing data with omnidirectional lighting at the press of a button. Observation can be performed immediately simply by selecting the optimal image, eliminating the hassle of determining the conditions. This product uses a free-angle observation system with XYZ motorised stage to enable tilted observation with easy field-of-view alignment, rotation, and oblique axis motion. Observation from various angles with high-resolution images is possible even for the inner surfaces of small die holes.
Using the high-resolution, fully-focused images captured at any angle or magnification allows users to take accurate sub-micrometre 3D measurements of the subtle surface irregularities on tablets.
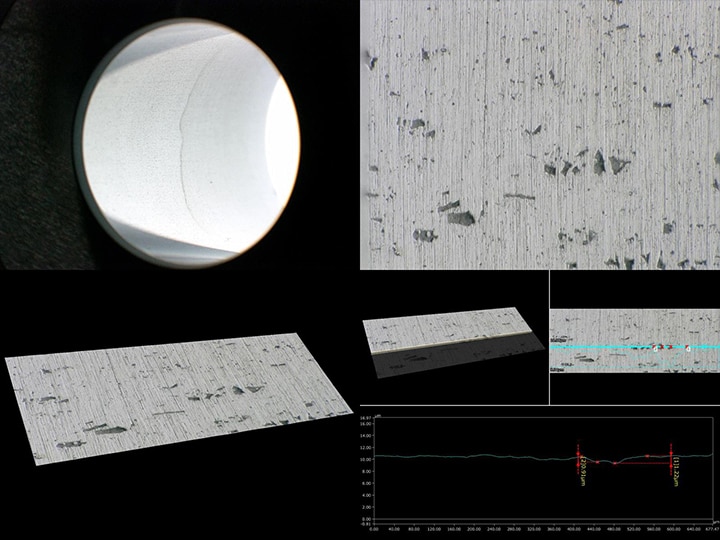
A Digital Microscope That Improves the Quality Assurance of Tablets
The VHX Series digital microscope can easily capture fully-focused images of tables and key parts of tableting machines at any angle or magnification. It is also able to take accurate 2D/3D measurements and output all this information automatically in a report, reducing the time and effort it takes to ensure the quality of the products.
For additional info or inquiries about the VHX Series, click the buttons below.