Laser Marking Systems / Laser Markers
How Does Laser Cleaning Work?
-
Tags:
- Laser Cleaning , Electric Vehicle , Battery
Cleaning metals, resin, and other materials is always in demand for a wide range of industries. With research increasing about how chemicals drastically increase climate change and health issues, laser cleaning is becoming necessary. Not only does it help the environment, but it also is the next step to keeping costs low and efficiency high. In the following, we’ll take a look at how KEYENCE’s laser marking systems outperform chemical cleaning and standard laser cleaning machines.
Exploring the Process of Laser Cleaning
Laser cleaning is the process of cleaning a surface by transforming its coating into gas. It begins with a high peak power laser with short pulse frequencies shooting into the surface of a film and heating it. Then, the coating is removed by vaporisation. Laser cleaning removes coatings such as enamel, wire sheath, or resin for various reasons. Resin coatings may be removed to review a defective mould. Wire sheath may need to be removed for a productive electrical connection.
Other notable aspects of the laser cleaning process include impressive precision and control over the intensity of the laser. Moreover, it surpasses traditional methods in essentially all regards.
This is especially true when it comes to its non-contact approach, which heavily mitigates the chances of damaging materials. Manufacturers who choose to clean with a laser also enjoy a dry cleaning process that doesn’t require water or chemicals.
Laser cleaning with KEYENCE's Hybrid Laser Marker MD-X Series is a more efficient, environmentally friendly, healthy, and cost-effective alternative than chemicals or any other conventional laser cleaner.
We’re here to provide you with more details.
Reach out today!
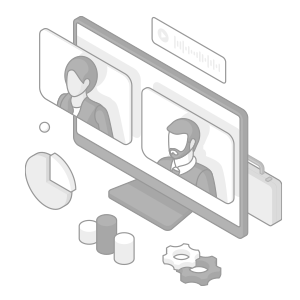
Key Components of Laser Cleaning Equipment
How does laser cleaning work exactly? In addition to the different types of laser cleaning machines, several universal critical components are involved. Laser cleaning technology would be nothing without the engineering behind each component.
A few essential aspects regarding the designs of laser cleaners include the following:
- Optic and beam delivery systems
- Different laser types and applications, such as fibre laser cleaning or UV laser cleaning
- Scanners for precise laser cleaning
- Multi-layered safety systems
- More innovative cooling abilities
- Exhaust system for fumes stemming from vaporised debris
Laser cleaning benefits are no secret, but that isn't to say the process doesn't come with its own due diligence. While it can significantly mitigate damage to surface material, a bit of preparation may still be needed.
Discover more about this product.
Click here to book your demo.
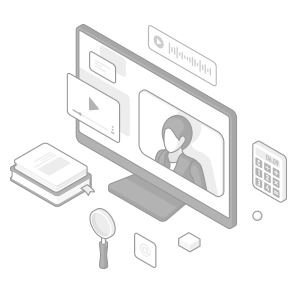
Laser Cleaning Applications
The best laser cleaning systems are KEYENCE’s Hybrid Laser Marker MD-X Series.
The Hybrid Laser Marker MD-X Series is perfect for cleaning out epoxy resin, abs resin, PBT, stainless steel, iron, aluminium, and rubber. It utilises a high peak power and a wavelength of 1064 nm to absorb any material needing to be removed. The high heat and precise beam-spot control eliminate the risk of damaging the internal circuit.
Get detailed information on our products by downloading our catalogue.
View Catalogue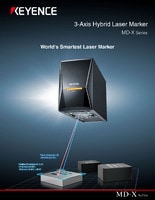
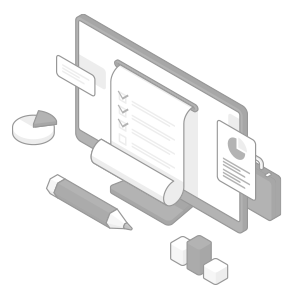
Laser Cleaning Versus Traditional Cleaning Methods
There are some apparent upsides to cleaning lasers compared to traditional methods. Of course, traditional takes on industrial cleaning will be around for a long time, but manufacturers are looking for ways to improve. The breakdown below offers a comparison between using a laser for cleaning and sticking to traditional practices.
Laser Cleaning
- Contaminants are vaporised and removed through the process of ablation.
- Makes use of a high-powered laser beam that avoids damaging the material’s surface.
- Minimal environmental impact and a dry cleaning experience.
- Precise control over the laser and coverage of surface area, in addition to the duration of laser pulses.
Traditional Cleaning
- Commonly relies on lots of water and chemical solutions to achieve an end result.
- Requires much more abrasive and physical labour, such as scrubbing and solvent cleaning.
- Effective for certain applications but isn’t nearly as efficient or cost-effective.
- Results tend to be less consistent and precise.
- Usually requires direct contact with the surface, which can easily lead to damage.
There is always room for improvement, but in light of laser surface cleaners, manufacturers are happy to make the switch. As laser cleaning equipment evolves with time, traditional cleaning methods will only become increasingly obsolete.
We’re here to provide you with more details.
Reach out today!
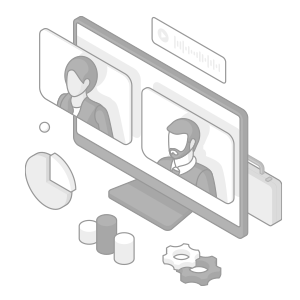
What Works Well for Laser Cleaning? What Doesn’t?
KEYENCE’s laser markers combat long work time and extra costs with their built-in camera, 3-Axis technology, and IP64 rating. The camera, alongside its displacement sensor, provides a full-field auto-focus function. The auto-focus positions and aligns the laser precisely onto the spot that is to be marked or cleaned. The 3-Axis system makes it possible to programme complex shapes into the laser cleaner without any runoff or distortion. Then, the IP64 rating allows for markings or a cleaning process to occur in production processes that are heavily contaminated with dirt and debris. Because of this, laser cleaning can happen efficiently and precisely without error or damage to the product.
On the other hand, conventional laser cleaners have blurred focus, position accuracy is poor, and set-up can take more time as alignment is repeatedly dialed in. Without a variable focal point, surfaces with height differences or curves cannot be effectively cleaned. As a result, uneven cleaning or damage to the surface occurs.
IP64 Rated Marking Head
The MD-X Series use a proprietary sealing method to securely protect optical components. This ensures that these components are not affected by factors such as dirt, dust, and water droplets, which provides environmentally resistant performance and allows for stable operation in even the harshest environments. These lasers have an enclosure rating equivalent to that of the fanless marking head of our MD-F Series fibre laser markers.
Get detailed information on our products by downloading our catalogue.
View Catalogue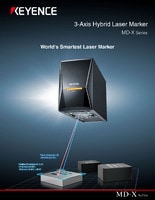
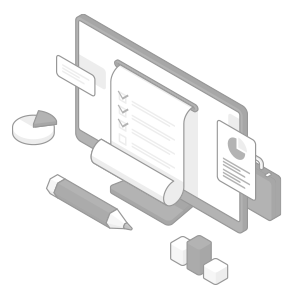
Cost Advantages of Laser Cleaning
KEYENCE’s laser cleaning systems require a one-time payment– buying the laser marker.
KEYENCE’s laser systems last four times longer than standard laser systems, so replacement fees are decreased when buying the MD-X. Moreover, labour costs decrease because of the AI engineering of KEYENCE’s systems. The MD-X can utilise the built-in internal camera for XY tracking of parts to eliminate the need for fixtures or precise part placement, so no time is wasted with manual setups. Lastly, since the MD-X do not use chemicals, this eliminates the cost of biohazard cleanup, regulatory fees, and Personal Protective Equipment (PPE).
Discover more about this product.
Click here to book your demo.
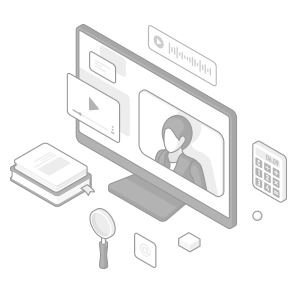
Environmental Advantages of Laser Cleaning
The reduction in environmental damage from using laser cleaning instead of chemicals is drastic.
Using chemicals is extremely harmful to the environment. Laser cleaning does not require any gathering of chemicals. Nor does laser cleaning emit gas into the air contributing to climate change or health issues. Further, laser cleaning does not require any disposal of chemicals. Laser cleaning does not produce any toxic waste or biohazards that may seep into water or air.
Chemicals are not used in laser cleaning with the MD-X, making it much more environmentally friendly.
We’re here to provide you with more details.
Reach out today!
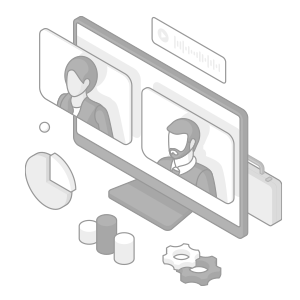
Safety With Laser Cleaning
Laser cleaning will not result in disease, burns, or irritation because it simply uses natural heat absorption. The MD-X are very easy to use, so there is a limited risk of injury. Furthermore, there is no risk of cross-contamination explosions because the MD-X do not use any toxic chemicals.
Alternatively, cleaning resin or metals with chemicals is inherently dangerous. Chemicals commonly used for cleaning procedures are nitric acid, hydrochloric acid, and phosphoric acid. These chemicals are extremely toxic to humans by contact and inhalation. The University of Massachusetts, Amherst, reports these chemicals can eat away at skin, eyes, respiratory systems, and gastrointestinal systems by contact. One of the chemicals used, phosphoric acid, can cause kidney failure, central nervous system effects, or even death. Additionally, inhaling these chemicals can irritate the lungs and lead to bronchitis. Because of the danger, hands, body, and mouth must be covered while working with these chemicals.
Curious about our pricing?
Click here to find out more.
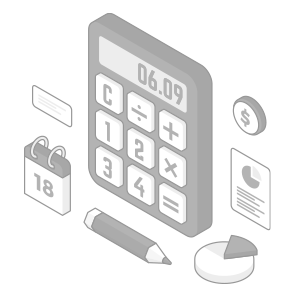
Convert to KEYENCE’s Laser Cleaning Today
You should not have to worry about environmental, health, or cost concerns when completing cleaning projects. Using KEYENCE’s laser markers can be your next step to feeling confident about your cleaning procedures. Learn more about our laser marking systems to find the best system for your project!
If you have any questions, ask KEYENCE—our knowledgeable team will get back to you quickly. We pride ourselves in our support for our customers throughout the selection process to operations with on-site operating instructions, along with industry-leading after-sales support.
We’re here to provide you with more details.
Reach out today!
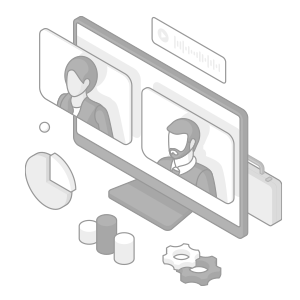