Laser Marking Systems / Laser Markers
Surface Finishing: Processes and Examples
-
Tags:
- Laser Ablation , Laser Engraving , Battery
Across a wide variety of products, industries, and manufacturing sectors, surface finishing is a common topic for several reasons. Featuring numerous production methods and outcomes, it’s an adaptable process that’s utilised for many applications.
From removing material to reshaping it within extreme detail, surface finishing plays a vital role in modern manufacturing. Although it isn’t a new concept, it is important to remain on the leading edge of the most current practices in surface finishing technologies.
What is Surface Finishing?
Surface finishing is a process that transforms the outer layer of a manufactured item. Several steps are involved when you surface finish a product or material. One of the main goals is to enhance or merely change the item's visual appeal. However, the technique goes far beyond this by improving mechanical properties and other quality factors. Depending on the process, certain characteristics of the material surface can be altered in unique ways.
While it may seem primarily aesthetic, surface finishing is vital to the performance and functionality of many different components. Not only can this be important for assembly, but it can also enhance bonding on coatings, corrosion resistance, and more.
Of course, a laser surface treatment isn’t needed for every component. Various considerations come into play before the surface finishing process is put into production. Several surface finishing techniques are popular for enhancing an item's general durability.
Discover more about this product.
Click here to book your demo.
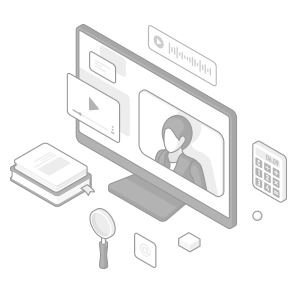
Top Surface Finishing Techniques for Improved Product Durability
For manufacturers looking to improve the durability of their products, you have multiple techniques to choose from. Metal surface finishing can also be accomplished through a variety of methods.
- Electroplating: With the help of an electrolyte solution, metal components are immersed in a metal coating. This is commonly done with nickel, zinc, or chromium, which leads to the submerged metal being plated to improve corrosion resistance. The technique is used for aesthetic reasons as well.
- Powder coating: Used to simulate a stronger surface than liquid coatings, powder coating technique includes an electrode, spray gun, and oven. Once the component is charged with the electrode, the powder is sprayed onto it, bringing an opposite charge. This causes the powder to stick to the part's surface, and the oven is used to seal in a strong bond.
- Anodising: It provides an attractive finish and acts as an added layer of protection against wear and tear. The same sentiment goes toward corrosion resistance, making it one of the most popular surface finish examples.
- Lasering: The biggest benefit of laser marking systems is their non-contact approach and pristine efficiency. They can easily remove surface contaminants and change the texture of a component without ever coming in contact with it. Due to this, laser surface finishing has many unique applications across a seemingly endless list of parts and materials.
- Plasma: A less expensive solution, plasma treatments focus on modifying chemical composition, carbonising surface contaminants, and etching materials. However, it should be noted that there’s less control compared to laser texturing.
Techniques such as powder coating and anodising are more traditional compared to the likes of laser cleaning or plasma treatments. Then again, if you compare the more modern processes, it's pretty evident why laser marking is becoming increasingly popular.
We’re here to provide you with more details.
Reach out today!
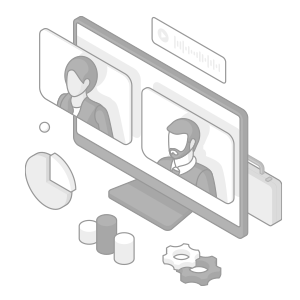
Innovations in Surface Finishing: Laser and Plasma Treatments
Traditional practices in surface finishing are still very viable and needed in global manufacturing. However, this industry is facing a demand for change stemming from consumers, competition, and shifting technology. To keep up with these changes, manufacturers must rely on more efficient techniques that benefit both time, money, and the end user.
For example, when comparing laser vs plasma cleaning, laser technology is clearly superior for one core reason. Its ability to move with extreme precision without the need for a guide mask makes it a much more efficient solution.
In addition, laser technologies are much more adaptable due to the many different laser mediums that are available. From fibre to CO2 to UV designs, manufactures have the ability to find the solution that will cover everything they need with a single unit.
While plasma treatments may not offer the same level of control or precision, they have their use cases. One of the most significant caveats when comparing these technologies is that plasma treatments are more prone to damaging a product than lasers.
Both are capable of non-contact, but plasma can easily modify the surface's chemical composition, potentially leading to damage. From surface modification to simple laser rust removal, both laser and plasma technologies have viability in the future of manufacturing.
Curious about our pricing?
Click here to find out more.
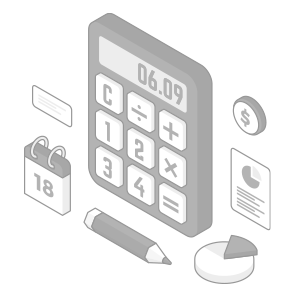
Choosing the Right Surface Finishing Process for Your Needs
Learning about the nuances of modern surface finishing can be overwhelming, but the type of materials and products you work with is a good place to start. The process you integrate into your daily operations should align with the type of products you work with.
You also shouldn’t feel restricted by the technique you choose. Using laser technology for surface finishing and cleaning means you can adapt from one material to the next. The process has common benefits, such as less downtime, improved operational efficiency, and higher-quality products. However, the techniques mentioned in this article shouldn’t be seen as one-size-fits-all.
Based on your needs, these few surface finish examples can be applied to different use cases:
- Linear: This type of pattern commonly features a small overlap between each line for a very efficient approach. It is known to be a quicker technique than others, as it covers the entire component’s surface.
- Grid: A grid pattern acts as an excellent finish before any adhesive or coating, and it takes less time to produce than a random pattern. However, it still takes longer to complete than a linear finish.
- Circular: Although this approach doesn't offer much adhesive reliability, it is known to hold a weaker bond due to the space between the circles. It also makes the component a bit harder to clean and doesn't cover the entire surface. In many cases, this technique is used for efficiency or aesthetic reasons.
If you aren't already using surface finishing techniques, you're missing out on an effective way to protect the integrity of your components. Thanks to more modern technologies and applications, taking a multi-faceted approach to surface finishing is easier than ever.
Whether you’re new to the technology or simply looking to upgrade your techniques, at KEYENCE, we have all the professional guidance you need. If you find yourself with any pressing questions or concerns, contact us for quick assistance.
We’re here to provide you with more details.
Reach out today!
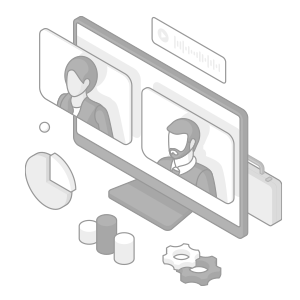