Industrial Laser Marking Systems / Laser Markers
What is Laser Annealing?
-
Tags:
- Laser Annealing , Medical , Aerospace
Lasers, with their versatile capabilities in engraving, etching, cutting, marking, and drilling, are a sought-after tool in the manufacturing industry. Among these techniques, laser annealing is one unlike any other that makes metals easier to process.
Laser annealing is a contact-free process that uses an infrared laser beam to rearrange the atoms on a metal’s surface. This rearrangement essentially draws the carbon content of a ferrous metal to the top, creating a jet-black contrasting mark with no damage to the surface or change to the material's mechanical properties. In this blog, we’ll discuss what laser annealing is, the process, its benefits, and many applications.
What Does Annealed Mean?
The word “anneal” means to heat and cool a material. It’s not specific to using a laser, but laser annealing is an efficient way of conducting it.
The original meaning of annealing was to “light on fire,” so the practice was likely used for centuries before electricity.
We’re here to provide you with more details.
Reach out today!
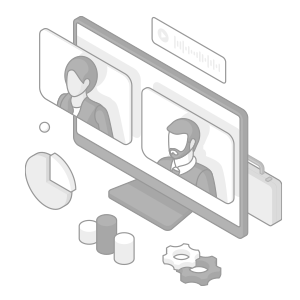
Laser Annealing Process and Steps
The annealing process involves numerous steps to ensure desired results are achieved:
- Step 1:
- An unfocused fibre laser beam shoots low-power conducted heat onto a surface area.
- Step 2:
- Metal changes from solid to liquid during the heating.
- Step 3:
- The laser is removed from the surface, and the metal changes from liquid to solid.
- Step 4:
- As the surface area cools, the atoms reorganise and change the crystal lattice.
- Laser Annealing End Result
- The end result of applying this de-focused beam, and the resulting low level of heat, to the surface of the part is a fully permanent mark that does not displace any material or change the surface characteristics.
Curious about our pricing?
Click here to find out more.
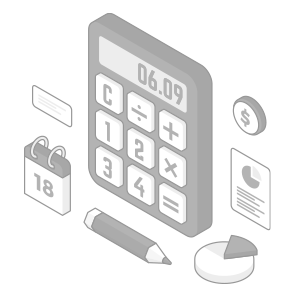
Laser Annealing vs. Other Laser Marking Methods
Laser annealing differs from other marking methods because of its process and outcome. Here are some of the main differences between each:
Focus
Laser annealing uses an unfocused beam for processing, whereas etching and engraving use a focused beam.This is what allows an annealed mark to produce contrast without damage to the material's surface.
Texture
Laser annealing does not leave any textured surface with its black mark. On the other hand, engraving leaves carved out marks. Etching will leave a slightly less "carved out" marking, and it generally produces much less contrast.
Discover more about this product.
Click here to book your demo.
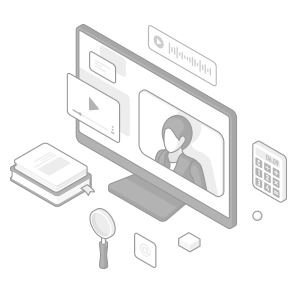
Laser Annealing Applications
The annealing process is used throughout many industries worldwide and for a variety of materials. The following are some of the most common:
Industries | Metals |
---|---|
Industries
|
Metals
|
We’re here to provide you with more details.
Reach out today!
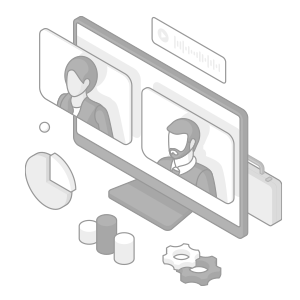
Laser Annealing Stainless Steel
UDI Requirements
The medical device industry is a strict regulatory industry that requires almost all devices to be marked with a Unique Device Identification (UDI) traceability mark. These UDIs require information, including product code, lot number, expiration date, serial number, and manufacturing date. However, since these medical devices are usually small and slim, it’s nearly impossible to mark all that information using words or numbers. Instead, 2D codes are frequently used because they easily store information and are read by computers.
The high contrast of black laser annealing stainless steel is ideal for 2D codes on medical devices for readability and permanency. Also, its non-textured mark doesn’t collect contaminants like dust, fluids, bacteria, or other debris.
In the medical field, maintaining hygiene and safety standards is paramount. When marking medical devices, the focus extends beyond the mark itself to prevent any introduction of contaminants during the marking process. Medical devices undergo rigorous sterilisation procedures before being used on patients.
Consider a scenario where the marking process introduces particles or contaminants to a medical device. This could jeopardize the device's cleanliness, potentially leading to patient infections or other complications. To avoid this, the marking process is subjected to stringent control and post-marking sterilisation testing. These tests confirm that marked devices remain untainted and safe even after undergoing sterilisation, ensuring patient well-being.
Curious about our pricing?
Click here to find out more.
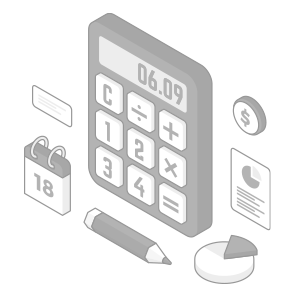
Laser Annealing Benefits
This process offers a number of benefits and advantages, making it a popular choice for manufacturers. Here are a few:
No Textured Surface Left Behind
Black laser annealing doesn’t leave behind any textured surface, whereas traditional marks from engraving or raised marks from etching do. Textures may be passable for certain industries, but black annealing’s non-textured mark is ideal in industries that require protection against contaminants like dust and debris. This is also true where extremely tight-fighting products require micron-level surface finishes that general marking styles could inhibit.
This factor is especially useful in the medical device industry because of parts’ repeated exposure to bacteria and contact with the human body. These parts must always be hygienic, and the black annealing ensures that.
Distortionless Marking
Laser black annealing uses an unfocused beam with only enough power to conduct heat and not heat the entire material. Because of these characteristics, the mark left behind is only surface level and doesn’t distort the material otherwise.
Discover more about this product.
Click here to book your demo.
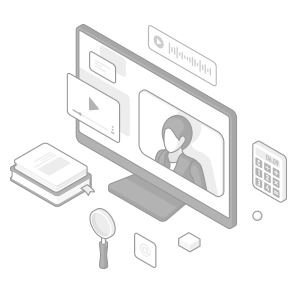
Laser Annealing Machine
Using a fibre laser marking machine works best for laser annealing. KEYENCE’s fibre laser is the 3-Axis Hybrid Laser MD-X Series. This laser has specialised features to make your annealing process even easier.
Hybrid Technology
The MD-X is versatile for a wide range of applications. The technology in these systems allows you to produce higher peak power through its oscillation structure. What does that mean? This provides you with higher contrast and less potential thermal impact than conventional laser markers.
3-Axis Control
3-axis control is a KEYENCE-specific feature that spans all laser machines. And it works especially well for laser annealing with the MD-F. The 3-axis control autofocuses to hit the target area exactly without any adjustment on the technician's end. This control achieves annealing over an area of 300 mm × 300 mm with a 42 mm variable focal distance.
For industries with strict guidelines about uniformity and readability, the 3-axis control ensures the processing has uniform line width and precision.
Ease of Use
Besides the powerful features provided by the MD-X, users find the system easy to use and intuitive. For example, the MD-X Series utilises an interior camera in the laser marking head, which can automatically identify a target’s shape. It also comes equipped with a built-in distance sensor which eliminates manual height adjustments and simplifies many processes.
Get detailed information on our products by downloading our catalogue.
View Catalogue
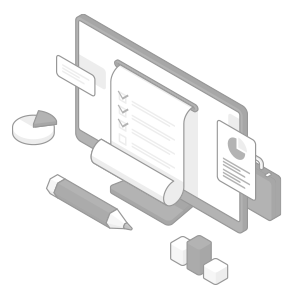
Want to Learn More About Lasers?
At KEYENCE, we specialise in all aspects of laser technology—especially laser annealing. Laser annealing can be your processing method for marking high contrast codes, making your metals stronger with anti-corrosion passivation, or making your metals softer for easier processing.
Ask KEYENCE for more information about laser annealing, our 3-Axis Fibre Laser MD-F Series, or any other laser processing. Our knowledgeable team is ready to help.
We’re here to provide you with more details.
Reach out today!
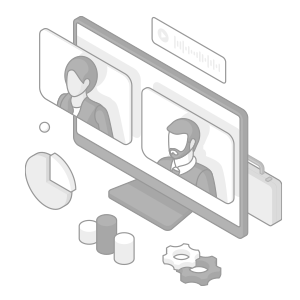